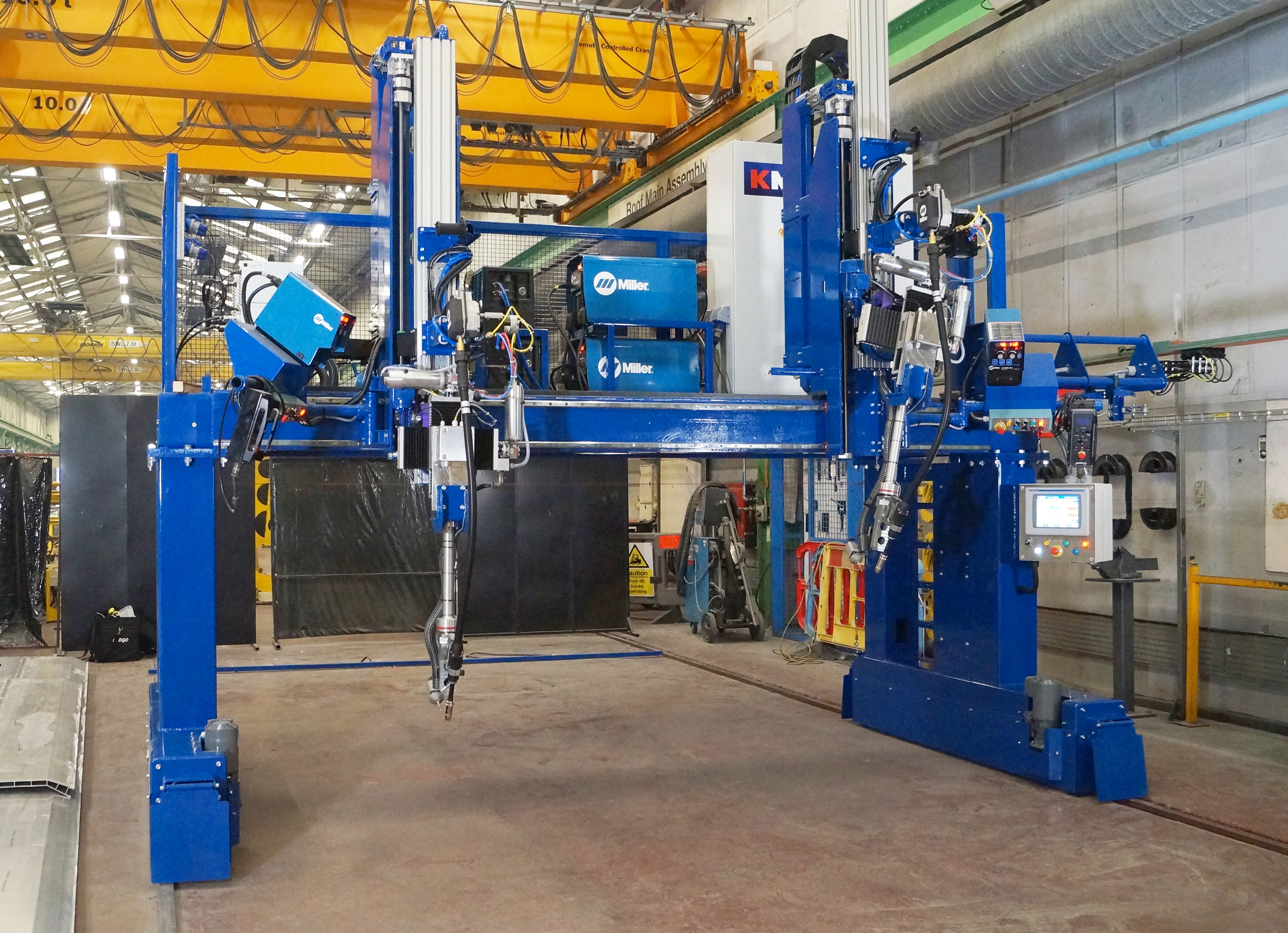
KM Tools Ltd has demonstrated its machine building capabilities by supplying a new welding gantry to Bombardier, the UK’s leading rail engineering and manufacturing company.
Bombardier is the only company in the UK with the capability to design, develop, manufacture, test and service trains. Producing multiple unit rail vehicles for a host of UK train operators, the business has to ensure adequate manufacturing capacity to support these extensive operations. Litchurch Lane has been producing railway rolling stock since the late 19th century, and now KM Tools Ltd is a part of the site’s modern era.
The welding gantry provided by KM Tools is a key machine in the production of train underframes and roofs. Sections of underframe/roof are held in jigs next to one another, ready for welding. With the expert help of operatives in protective gear, the welding gantry passes over, its two heads carrying out high-quality welds across the length of each seam. Once one side of the underframe/roof section is welded, the jig is rotated 180 degrees and the process repeated for the opposite side.

The welding gantry provided by KM Tools is a key machine in the production of train underframes and roofs.
Adrian Degg, Group Engineering Director at KM Tools Ltd, was instrumental in the project: “We are primarily a machine builder, working with our customers to provide specialist equipment to support OEM production lines. We had previously supplied a wide range of jigs and fixtures to support Bombardier’s production activities, so when the time came to add a new welding gantry at the facility, we were ready to offer a solution.”
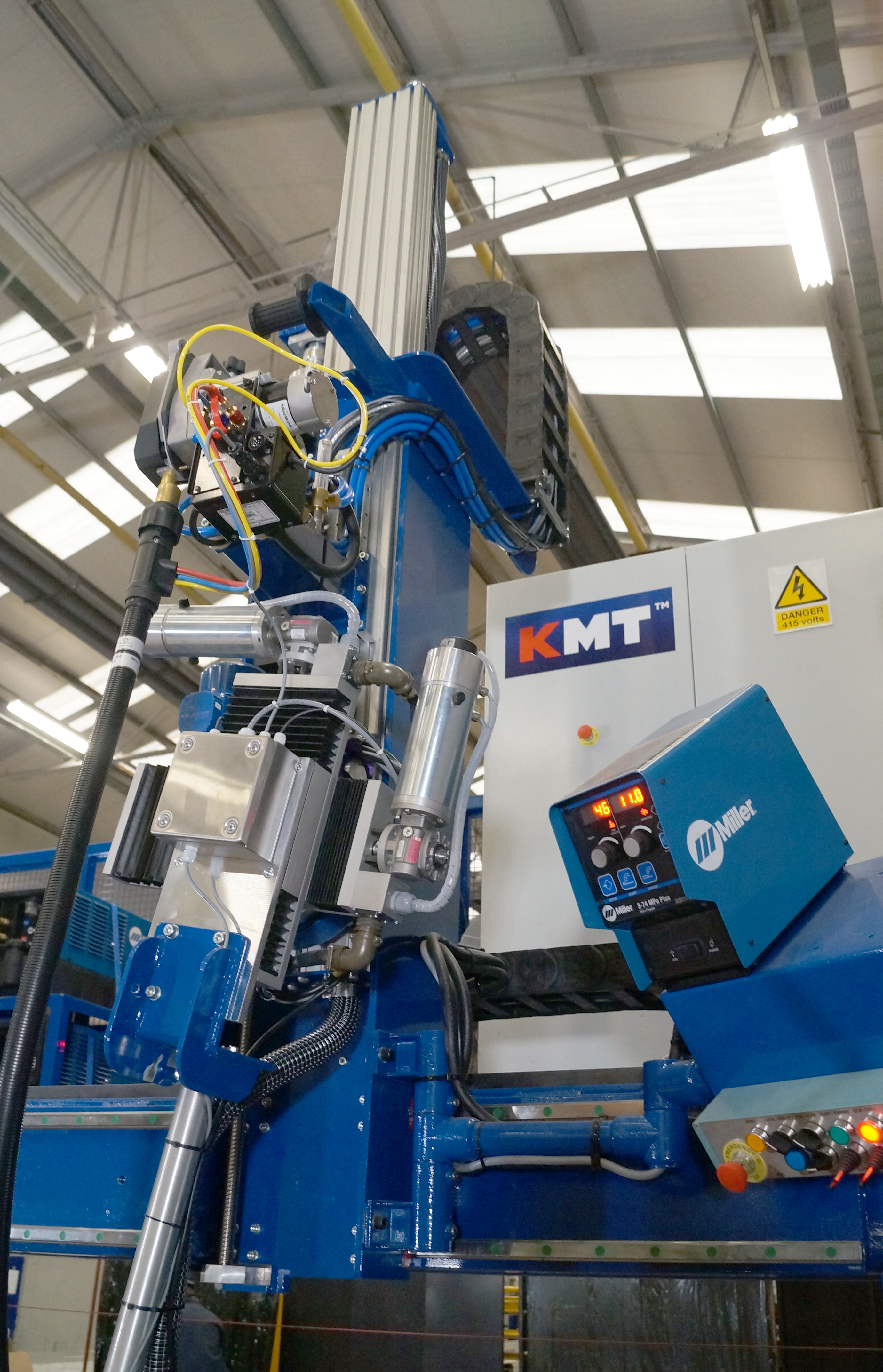
Bombardier required a new welding gantry that closely matched those already operational on-site.
Bombardier required a new welding gantry that closely matched those already operational on-site. KM Tools offered to reverse engineer a new machine to the required specification, offering a reduced lead time and increased value compared to its competitors. The welding gantry would need to be installed and operational by mid-February, 2020.
KM Tools managed the entire build process. After inspecting an existing machine, engineers replicated the frame and installed two welding heads with seam tracking. Seam tracking is controlled via an articulated mechanical contact (See Photo 5) mounted on the head, which moves the welder up and down or side to side depending on its current position relative to the seam. Allen-Bradley controls were installed on the machine, with programmable safety features. KM Tools made sure the software and user interface were almost identical to other machines to ensure operator familiarity.

KM Tools made sure the software and user interface were almost identical to other machines to ensure operator familiarity.
The machine was finished within seven weeks, with installation completed before the deadline. The machine is now operational, boosting welding capacity at the site.
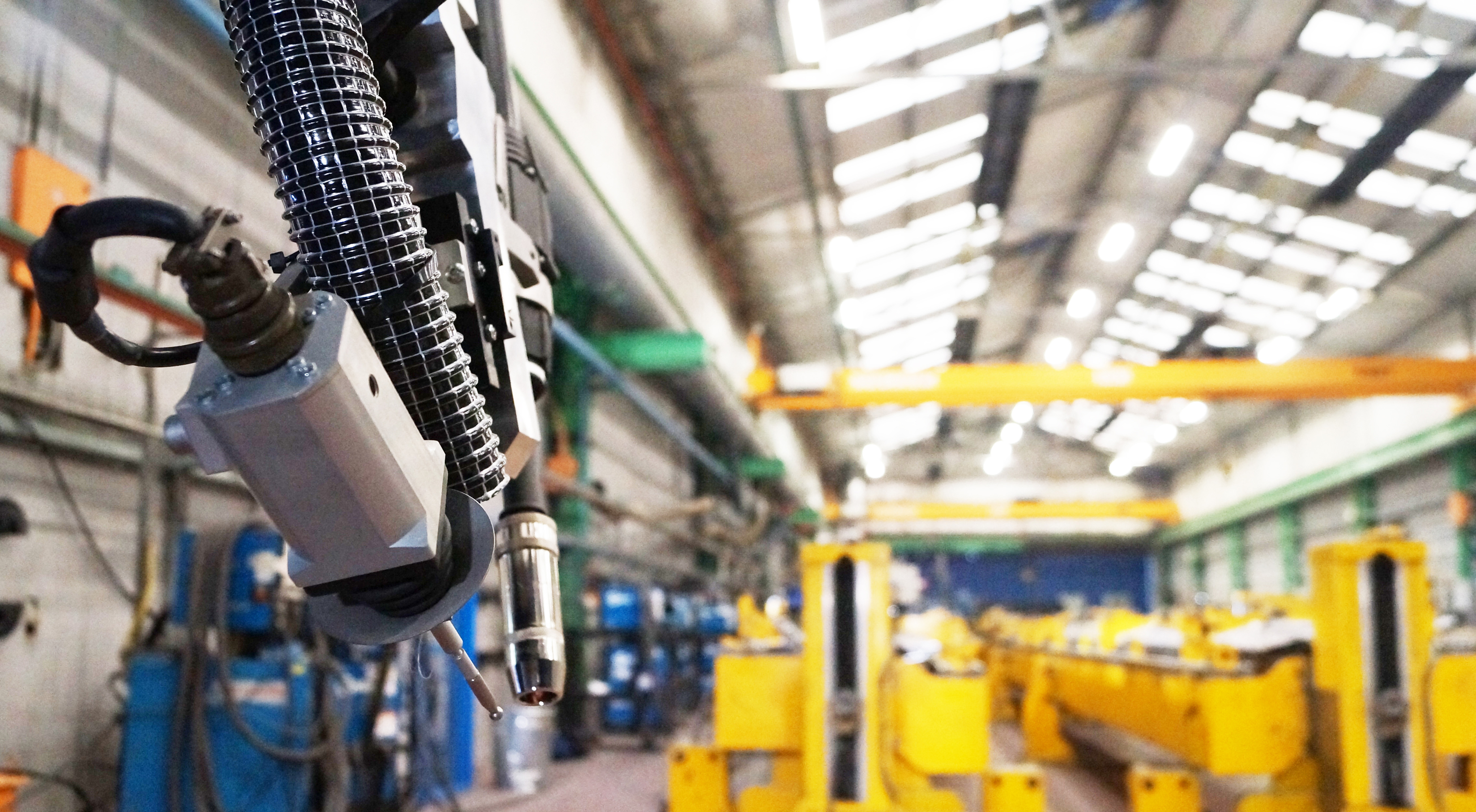
Seam tracking is controlled via an articulated mechanical contact mounted on the head, which moves the welder up and down or side to side depending on its current position relative to the seam.
Adrian concludes: “We enjoyed working on this machine, and it has operated without issue since it was commissioned. We have KM Tools engineers on-site to quickly react to any issues, so there is extra assurance there. We’re used to meeting the needs of leading OEMs across multiple industries, which has greatly aided our work at Bombardier. By utilising this experience and offering a turnkey solution – we were able to deliver an ideal, value-added machine quickly.”
Recent Comments